실리콘 웨이퍼란?
실리콘은 회색의 부서지기 쉬운 4원자의 화학 원소입니다. 이는 지구 표면의 27.8%를 차지하며, 자연에서 산소 다음으로 가장 풍부한 원소입니다. 규소를 함유한 가장 흔한 재료로는 석영, 아가테, 부싯돌, 해변 모래 등이 있습니다. 이는 시멘트, 벽돌, 유리와 같은 건축 자재의 주요 성분이기도 합니다. 또한 실리콘은 반도체와 마이크로칩을 만드는 가장 흔한 재료이기도 합니다. 아이러니하게도 실리콘은 그 자체로는 전기를 잘 전도할 수 없지만, 저항을 정확한 사양으로 제어하기 위해 도펀트를 정확하게 흡수할 수 있습니다.
반도체를 만들기 위해서는 실리콘을 웨이퍼로 변화시켜야 하는데, 이것이 실리콘 웨이퍼입니다. 이것은 실리콘 잉곳의 성장과 함께 시작됩니다. 하나의 실리콘 결정은 3차원 주기적 패턴으로 배열된 원자로 구성되며, 이 원자는 재료 전체에 걸쳐 확장됩니다. 폴리실리콘 결정은 반도체 장치에 사용할 수 없는 오리엔테이션이 다른 수많은 작은 단일 결정(크리스탈)에 의해 형성됩니다.
실리콘 웨이퍼 제조
실리콘 잉곳(실리콘 잉곳)을 기르는 데 걸리는 시간은 다양한 요인에 따라 다릅니다. 전체 75% 이상의 단일 결정 실리콘 웨이퍼가 CZ(Czochralski) 방식을 통해 성장합니다. CZ 잉곳 성장은 새로운 다결정 실리콘 덩어리를 필요로 합니다. 이 덩어리는 도펀트(dopants)라고 불리는 소량의 그룹 III, 그룹 V 원소와 함께 석영(quartz) 도가니에 놓이게 됩니다. 첨가된 도펀트는 다 자란 잉곳에 필요한 전기적 특성을 제공하게 됩니다. 가장 흔한 도펀트는 붕소, 인, 비소, 안티몬입니다. 도판트에 따라 잉곳은 P, N타입 잉곳(보론: P타입, 인, 안티몬, 비소: N타입)이 됩니다.
잉곳 성장
잉곳을 성장시키기 위한 첫 번째 단계는 실리콘의 용융점보다 높은 1420°C까지 실리콘을 가열하는 것입니다. 다결정과 도판트 조합이 액화되면 하나의 실리콘 결정인 씨앗이 용융물 위로 올라와 표면에 거의 닿지 않게 됩니다. 씨앗은 완성된 잉곳에서 요구되는 결정 오리엔테이션을 갖습니다. 도핑 균일성을 얻기 위해 녹은 실리콘의 씨 결정과 도가니를 반대 방향으로 회전시킵니다. 일단 시스템이 결정 성장을 위한 적절한 조건에 도달하면, 천천히 씨앗 결정체를 용융에서 꺼내줍니다. 그리고 씨앗 결정체를 빠르게 잡아당기는 것으로 성장이 시작됩니다. 이렇게 하면 성장 과정 시작 시, 씨앗 내의 결정 결함 수를 최소화할 수 있습니다.
이후, 당기는 속도를 줄여 크리스탈의 직경을 증가시킵니다. 원하는 직경이 확보되면 성장 조건이 안정화되어 해당 직경이 유지되게 됩니다. 씨앗이 용융물 위로 천천히 올라갈 때, 씨앗과 용융물 사이의 표면 장력은 실리콘의 얇은 막이 씨앗에 달라붙어 식도록 만들어 줍니다. 냉각이 진행되는 동안 녹은 실리콘의 원자들은 씨앗의 결정 구조에 스스로 방향을 잡습니다.
슬라이싱
잉곳이 완전히 성장하면 최종 실리콘 웨이퍼의 목표 직경보다 약간 큰 크기로 접힙니다. 잉곳에는 오리엔테이션을 나타내기 위해 홈이나 납작하게 자른 부분이 있습니다. 여러 번 검사를 통과한 후, 잉곳 슬라이싱이 진행됩니다. 실리콘의 단단함 때문에 다이아몬드 엣지 톱으로 실리콘 웨이퍼를 조심스럽게 자릅니다(이때는 목표 사양보다 약간 두껍게 자르게 됩니다). 다이아몬드 엣지 톱은 웨이퍼의 손상, 두께 변화, 보우와 워프 결함을 최소화하는 데에도 도움이 됩니다.
웨이퍼를 슬라이스한 후 래핑 공정이 시작됩니다. 웨이퍼를 래핑하면 웨이퍼 앞뒷면의 톱자국과 표면 하자가 제거됩니다. 이는 웨이퍼를 얇게 해주고 슬라이싱 공정으로 인해 웨이퍼에 쌓인 응력을 해소해 줍니다. 실리콘 웨이퍼를 래핑한 후, 엣칭과 세척 과정을 거칩니다. 수산화 나트륨 또는 아세트산과 질산은 래핑 중에 발생할 수 있는 미세한 균열/표면 손상을 완화해줍니다. 중요한 모서리 그라인딩 절차는 가장자리를 둥글게 만드는 과정인데, 이는 나머지 제조 단계에서의 파손 가능성을 크게 줄여줍니다. 또한 나중에 장치 제조업체가 웨이퍼를 사용할 때도 파손 방지에 도움이 됩니다.
모서리를 라운딩한 후, 최종 사용자의 사양에 따라 종종 모서리에 추가 광택 단계를 거치게 됩니다. 이를 통해 전체적인 청결도를 개선하고 파손을 최대 400%까지 줄일 수 있습니다.
클리닝
광택 연마
대부분의 프라임 그레이드 실리콘 웨이퍼는 점진적으로 미세한 슬러리나 광택 화합물을 사용하여 2~3단계의 광택 과정을 거칩니다. 대부분의 경우 웨이퍼는 앞면만 광택 처리됩니다(단, 양면 광택 처리된 300mm 웨이퍼는예외입니다). 광택을 내면 거울 마감이 만들어집니다. 또한 광택제는 장치 제작에 사용할 면을 구분합니다. 이 표면에는 지형, 미세 균열, 긁힘, 잔여 작업의 손상이 없어야 합니다.
광택 공정은 스톡 제거와 최종 화학적 기계적 광택(CMP)의 두 단계로 이루어집니다. 두 공정 모두 광택 패드와 광택 슬러리를 사용합니다. 스톡 제거 공정은 매우 얇은 실리콘 층을 제거하며, 손상이 없는 웨이퍼 표면을 만드는 데 필요합니다. 반면 최종 광택제는 어떤 물질도 제거하지 않습니다. 스톡 제거 공정 중에 웨이퍼 표면에 연무가 형성되므로 추가적인 광택 단계를 통해 웨이퍼에 미러 마감을 해야 합니다.
광택이 끝나면 실리콘 웨이퍼는 긴 세척 수조를 사용하는 최종 세척 단계로 진행됩니다. 이 공정은 표면의 입자, 미량의 금속, 잔여물을 제거합니다. 때로는 그보다 더 작은 입자를 제거하기 위해 뒷면 스크럽(Thinning)이 이루어지기도 합니다.
포장
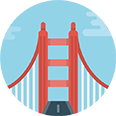
베이 지역 (Bay Area) 어디든 4시간 이내.
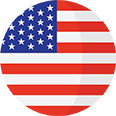
미국에서는 1일 이내.
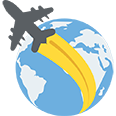
국제적으로 3일 이내.