Silicon carbide (SiC) was discovered in 1893 as an industrial abrasive for grinding wheels and automotive brakes. About midway through the 20th century, SiC wafer uses grew to include in LED technology. Since then, it has expanded into numerous semiconductor applications due to its advantageous physical properties. These properties are apparent in its wide range of uses in and outside the semiconductor industry. With Moore’s Law appearing to reach it’s limit, many companies within the semiconductor industry is looking towards silicon carbide as the semiconductor material of the future.
SiC can be produced using multiple polytypes of SiC, although within the semiconductor industry, most substrates are either 4H-SiC, with 6H- becoming less common as the SiC market has grown. When referring to 4H- and 6H- silicon carbide, the H represents the structure of the crystal lattice. The number represents the stacking sequence of the atoms within the crystal structure. This is described in the SVM capabilities chart below.
Advantages of Silicon Carbide
Hardness
There are numerous advantages to using silicon carbide over more traditional silicon substrates. One of the major advantages is its hardness. This gives the material many advantages, in high speed, high temperature and/or high voltage applications.
Silicon carbide wafers have high thermal conductivity, which means they can transfer heat from one point to another well. This improves its electrical conductivity and ultimately miniaturization, one of the common goals of switching to SiC wafers.
Thermal capabilities
Silicon carbide substrates also have a low coefficient for thermal expansion. Thermal expansion is the amount and direction a material expands or contracts as it heats up or cools down. The most common explanation is ice, although it behaves opposite of most metals, expanding as it cools and shrinking as it heats up. Silicon carbide’s low coefficient for thermal expansion means that it does not change significantly in size or shape as it is heated up or cooled down, which makes it perfect for fitting into small devices and packing more transistors onto a single chip.
Another major advantage of these substrates is their high resistance to thermal shock. This means they have the ability to change temperatures rapidly without breaking or cracking. This creates a clear advantage when fabricating devices as it is another toughness characteristic that improves the lifetime and performance of silicon carbide in comparison to traditional bulk silicon.
On top of its thermal capabilities, it is a very durable substrate and does not react with acids, alkalis or molten salts at temperatures up to 800°C. This gives these substrates versatility in their applications and further assists their ability to out perform bulk silicon in many applications.
Its strength at high temperatures also allows it to safely operate at temperatures over 1600°C. This makes it a suitable substrate for virtually any high temperature application.
SVM Silicon Carbide Specifications:
**While SVM may still occasionally have 6H-SiC wafers available, these are being phased out industry-wide for the more versatile 4H-SiC. Please let us know your requirements and we can check on the availability.**
4H-SiC | **6H-SiC** | |
---|---|---|
Diameter | 50mm (2"), 76mm (3"), 100mm (4"), 150mm (6") | 50mm (2") & 100mm (4") |
Type/Dopant | N/Nitrogen / intrinsic / HPSI | N/Nitrogen / intrinsic / HPSI |
Resistivity | .012 - .028 ohm*cm | >.00001 ohm*cm |
Thickness | 250um - 15,000um (15mm) | 250um - 15,000um (15mm) |
Surface Finish | Single or double side polished | Single or double side polished |
Stacking Sequence | ABCB | ABCACB |
Dielectric Constant | 9.6 | 9.66 |
Electron Mobility | 800 cm2/V*S | 400 cm2/V*S |
Density | 3.21 · 103 kg/m3 | 3.21 · 103 kg/m3 |
Not finding what you’re looking for?
If you have a question or would like to request a quote, please contact a member of our Sales Team.
Contact UsInventory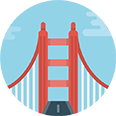
Anywhere in the Bay Area within 4 hours.
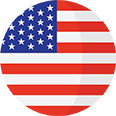
In the United States within 1 day.
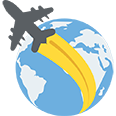
Internationally within 3 days.