Cavity Silicon-on-Insulator (C-SOI)-Wafer sind eine innovative SOI-Technologie, bei der der Griff-Wafer vorgeätzte Hohlräume enthält. Die Hohlräume, manchmal auch als Muster bezeichnet, werden nach innen geklebt, so dass im Inneren der Wafer vergrabene Hohlräume entstehen. Diese haben viele Anwendungen in der MEMS-Technologie (mikroelektromechanische Systeme) und bieten viele Vorteile gegenüber der Bulk-Silizium-Mikrobearbeitung und der traditionellen SOI-Technologie. Ein großer Vorteil dieser Technologie ist die geringere parasitäre Kapazität zwischen dem Bauelement und der Griffschicht des SOI-Wafer. Dadurch können die Geräte viel effizienter arbeiten. Die Verwendung tieferer Kavitäten und kleinerer Bondflächen kann die parasitäre Kapazität weiter verringern, sofern andere Variablen kontrolliert werden.
Wenn Sie daran interessiert sind, C-SOI von SVM zu erwerben, nehmen Sie bitte Kontakt mit uns auf, um ein Exemplar unserer Designregeln für Hohlraumschichten zu erhalten.
C-SOI-Fertigungsprozess:
Die Herstellung von SOI mit Hohlräumen unterscheidet sich geringfügig von der herkömmlichen SOI-Fertigung, da die Bildung von Hohlräumen zu unterschiedlichen Vorteilen und potenziellen Nachteilen führt. Dieser Prozess wurde in erster Linie für den Einsatz in der MEMS-Industrie optimiert, obwohl er das Potenzial hat, die Funktion von Bauteilen in einer Reihe von Anwendungen zu verbessern.
In einigen Fällen werden Säulen in die Kavitäten geätzt, um die Gesamtdickenvarianz (TTV) und die Funktion der Bauteile zu verbessern. Durch das Einfügen von Pfeilern entstehen qualitativ hochwertigere Siliziummembranen (die Siliziumschicht über dem Hohlraum) und die Gleichmäßigkeit des Hohlraums wird verbessert, während ein höheres Seitenverhältnis die Leistung des Bauelements und die Prozesskontrolle während der Lithografie verbessert. Da die Größe der Kavitäten die Fähigkeit zur Ausdünnung der Bauelementeschicht verändert, kann die Einbeziehung von Säulen die TTV und die Integrität der Wafer beeinflussen. Wenn diese nicht klar definiert sind, kann dies die Resonanzeigenschaften beeinträchtigen und dazu führen, dass verschiedene Regionen des Substrats mit unterschiedlichen Amplituden schwingen, was zu einer sehr hohen TTV, Fehlfunktionen der Bauelemente und Bruch führen kann.
Schritt für Schritt Prozessablauf:
- Unbehandeltes Siliziumsubstrat vorbereiten
- Die Herstellung beginnt mit einer Reinigung, um alle Oberflächenpartikel zu entfernen, die während der Herstellung Probleme verursachen könnten.
2. Bringen Sie eine Fotomaske auf das Griffsubstrat auf, um die Kavitäten, die in den Wafer geätzt werden sollen, klar zu definieren
- Um das Muster zu erstellen, wird ein Plasmapolymerfilm auf das Substrat aufgebracht. In diesem Schritt werden auch die Säulen definiert, falls sie verwendet werden sollen. Bei vielen Projekten ermöglicht die Verwendung von Pfeilern tiefere Kavitäten und ein höheres Seitenverhältnis, während gleichzeitig das Risiko von Kerben und anderen Problemen, die beim Ätzen oder bei der Sekundärverarbeitung auftreten können, begrenzt wird.
3. Tiefes reaktives Ionenätzen (DRIE) entfernt Material, um Hohlräume zu schaffen, gefolgt von einem Fotolackstreifen
- Beim DRIE-Ätzen werden sehr präzise Mengen an Silizium abgetragen, um die von der Fotomaske definierten Hohlräume zu erzeugen. Bereiche, die nicht von der Fotomaske bedeckt sind, werden durch Ionenbeschuss geätzt, um die gewünschten Kavitäten zu erzeugen. Während dieses Schritts werden Stützpfeiler in die Hohlräume geschnitten. Das DRIE-Verfahren ist wegen seiner gleichmäßigen Ätzrate und seiner allgemeinen Einfachheit am weitesten verbreitet. Da hierfür flüssige Ätzmittel erforderlich sind, wird dieser Prozess mit der Weiterentwicklung der Technologie weiter optimiert.
- Die Ätzrate variiert zwischen 0,8 μm/min und 1,25 μm/min, je nach Breite und Seitenverhältnis der Kavitäten. Nach dem Ätzen der Kavitäten wird die Fotomaske abgestreift, so dass ein strukturierter Wafer zurückbleibt.
4. Sauberes Substrat
- Nach dem Ätzen des Wafer ist es wichtig, überschüssiges Silizium und Photoresist zu entfernen. Dies verhindert Probleme beim Bonden.
5. Abscheidung einer isolierenden Schicht
- Thermisches Oxid (oder ein alternativer Isolator) kann vor oder nach dem Ätzen abgeschieden werden, in manchen Fällen auch beides, je nach den Anforderungen des Projekts. Wenn die Oxidschicht vor dem Ätzen aufgebracht wird, dringt das Ätzen durch die Oxidschicht bis hinunter zum Substrat. Dies kann je nach Tiefe zu Hohlraumwänden führen, die keinerlei Isolierung aufweisen.
- Wenn die Oxidschichten nach dem Ätzen wachsen, bilden sich an den Ecken des Hohlraums kleine Erhebungen. Die Höcker sind zwischen 5-20 μm hoch und variieren mit der Dicke der Isolierschicht. Dies führt auch zu einer leichten Abrundung aller Ecken aufgrund der Natur der Siliziumdioxidbildung.
6. Verbunden mit Cap-Wafer (Geräteschicht des SOI-Wafer)
- Die besten Ergebnisse erzielen Sie, wenn Sie CSOI-Wafer direkt im Vakuum verkleben. Diese Wafer werden mit Wasser oder einem ähnlich neutralen Material verbunden und dann bei 1100°C bis zu 2 Stunden lang getempert, um die Verbindung zu verfestigen. Nach dem Ausglühen ist kein Klebstoff mehr vorhanden, der die Verbindung zwischen den Wafern erleichtert. Durch die Durchführung im Vakuum wird verhindert, dass die Hohlräume überschüssige Luft und andere Verunreinigungen enthalten. Dies trägt auch dazu bei, dass die Konsistenz beim Ausdünnen des Cap-Wafer erhalten bleibt, da der Druck in den Kavitäten über das gesamte Substrat hinweg gleichmäßig ist.
7. Dünnen Sie den oberen (Bauelement-)Wafer mit CMP/KOH (Kaliumhydroxid)-Ätzung aus
- Der Cap-Wafer muss auf die gewünschte Schichtdicke des Bauelements ausgedünnt werden. Dies ist der variabelste Schritt bei der CSOI-Herstellung, da die Ausdünnungsrate und -qualität stark von der Qualität der Verbindung sowie den physikalischen Eigenschaften der Hohlräume abhängt. Natürlich vibrieren die Siliziummembranen in dieser Phase, was zu einer variablen TTV in diesen Bereichen führt. Wenn Sie die vorherigen Herstellungsschritte im Vakuum durchführen, können Sie viele dieser Probleme vermeiden.
8. Sekundärverarbeitung, je nach Anwendung und Gerätespezifikation
- Im Gegensatz zu herkömmlichen SOI-Wafern können CSOI-Wafer nach der Herstellung einer sekundären Rückseitenbearbeitung unterzogen werden. Das bedeutet extrem dünne Membranen, empfindliche Oberflächenstrukturen, Metallfilmstapel und generell mehr Designfreiheit als bei herkömmlichen SOI-Wafern.
Vorteile von C-SOI-Wafern:
- Reduziert die Kosten für das Gerät ohne Kompromisse bei der Präzision oder Qualität.
- Reduziert die Größe des Geräts. Der Einbau von Hohlräumen ermöglicht extrem dünne Griff/BOX/Geräteschichten.
- Das Bonden von strukturierten Wafern ermöglicht eine doppelseitige Bearbeitung der SOI-Schicht und eröffnet viele Möglichkeiten im Bereich der Mikromechanik.
Anwendungen:
Vorgeätzte SOI-Wafer sind eine geeignete Plattform für vertikal und horizontal bewegte Strukturen in verschiedenen Anwendungen, wie kapazitive Trägheitssensoren, Drucksensoren, Mikrofone und mikrofluidische Geräte.
Die meisten Anwendungen finden sich derzeit in MEMS- und Sensoranwendungen, aber diese Wafer können jede SOI-Wafer-Anwendung verbessern.
Sie finden nicht, wonach Sie suchen?
Wenn Sie eine Frage haben oder ein Angebot anfordern möchten, wenden Sie sich bitte an ein Mitglied unseres Vertriebsteams.
Kontaktieren Sie unsInventar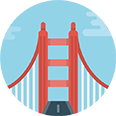
Überall in der Bay Area innerhalb von 4 Stunden.
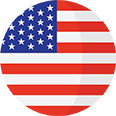
In den Vereinigten Staaten innerhalb von 1 Tag.
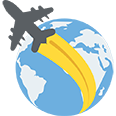
International innerhalb von 3 Tagen.