Les plaquettes de silicium sur isolant à cavité (C-SOI) sont une technologie SOI de pointe dans laquelle la plaquette de poignée contient des cavités gravées au préalable. Les cavités, parfois appelées motifs, sont collées vers l'intérieur, ce qui donne des cavités enfouies à l'intérieur des plaquettes. Ces cavités ont de nombreuses applications dans la technologie des systèmes microélectromécaniques (MEMS) et surfrent de nombreux avantages par rapport au micro-usinage du silicium en vrac, ainsi que par rapport à la technologie SOI traditionnelle. L'un des principaux avantages de cette technologie est la réduction de la capacité parasite entre le dispositif et la couche de poignée de la plaquette SOI. Cela permettra aux dispositifs de fonctionner beaucoup plus efficacement. L'utilisation de cavités plus prsurondes et de zones de collage plus petites peut réduire davantage la capacité parasite, à condition que d'autres variables soient contrôlées.
Si vous êtes intéressé par l'achat de C-SOI de SVM, veuillez nous contacter pour obtenir une copie de nos règles de conception de la couche de cavité.
Processus de fabrication du C-SOI :
La fabrication de SOI à cavités diffère légèrement de la fabrication de SOI plus conventionnelle, car la formation de cavités présente des avantages et des inconvénients potentiels différents. Ce processus a été principalement optimisé pour une utilisation dans l'industrie des MEMS, bien qu'il ait le potentiel d'améliorer la fonction des dispositifs dans une gamme d'applications.
Dans certains cas, des piliers sont gravés dans les cavités pour améliorer la variance de l'épaisseur totale (TTV) et la fonction du dispositif. L'inclusion de piliers crée des diaphragmes en silicium de meilleure qualité (la couche de silicium au-dessus de la cavité) et améliore l'uniformité de la cavité, tandis que des rapports d'aspect plus élevés amélioreront les performances du dispositif et le contrôle du processus pendant la lithographie. Étant donné que la taille des cavités modifie la capacité à amincir la couche du dispositif, l'inclusion de piliers peut influencer le TTV et l'intégrité des plaquettes. Si ceux-ci ne sont pas clairement définis, ils peuvent affecter les propriétés de résonance et faire vibrer différentes régions du substrat à des amplitudes différentes, ce qui peut entraîner un TTV très élevé, un dysfonctionnement du dispositif et des ruptures.
Flux de processus étape par étape :
- Préparation du substrat de silicium nu
- La fabrication commence par un nettoyage afin d'éliminer toute particule de surface susceptible de créer des problèmes lors de la fabrication.
2. Appliquez un photomasque sur le substrat de la poignée pour définir clairement les cavités qui seront gravées dans la plaquette.
- Pour créer le motif, un film de polymère plasma est appliqué sur le substrat. Au cours de cette étape, les piliers sont également définis s'ils doivent être utilisés. Pour de nombreux projets, l'utilisation de piliers permet d'obtenir des cavités plus prsurondes et des rapports d'aspect plus élevés, tout en limitant le risque d'entailles et d'autres problèmes pouvant survenir lors de la gravure ou du traitement secondaire.
3. La gravure ionique réactive prsuronde (DRIE) enlève le matériau pour créer des cavités, suivie d'une bande de résine photosensible.
- La gravure DRIE enlève des quantités très précises de silicium pour créer des cavités définies par le masque photographique. Les zones non couvertes par le photomasque sont gravées par bombardement ionique pour créer les cavités souhaitées. Au cours de cette étape, des piliers de soutien sont découpés dans les cavités. La méthode DRIE est la plus courante en raison de l'uniformité de son taux de gravure élevé et de sa simplicité générale. Comme il nécessite des agents de gravure liquides, ce procédé continuera à être optimisé au fur et à mesure que la technologie se développera.
- La vitesse de gravure varie de 0,8 μm/min à 1,25 μm/min en fonction de la largeur et du rapport d'aspect des cavités. Après la gravure des cavités, le photomasque est décapé, laissant une plaquette à motifs.
4. Nettoyer le substrat
- Après la gravure de la plaquette, il est important d'éliminer tout excès de silicium et de résine photosensible qui pourrait subsister. Vous éviterez ainsi des problèmes lors du collage.
5. Dépôt d'une couche isolante
- L'oxyde Lermique (ou un autre isolant) peut être déposé avant ou après la gravure, et dans certains cas les deux, en fonction des exigences du projet. Si le dépôt d'oxyde est effectué avant la gravure, celle-ci traversera la couche d'oxyde jusqu'au substrat ; la gravure peut également enlever une partie du substrat sous-jacent. Il peut en résulter des parois de cavité dépourvues de tout isolant, en fonction de la prsurondeur.
- Lorsque les couches d'oxyde se développent après la gravure, de petites bosses se forment dans les coins de la cavité. Ces bosses ont une hauteur comprise entre 5 et 20 μm et varient en fonction de l'épaisseur du film isolant. Il en résulte également un léger arrondi de tous les coins en raison de la nature de la formation du dioxyde de silicium.
6. Collé avec la plaquette de couverture (couche de dispositif de la plaquette SOI)
- Pour obtenir les meilleurs résultats, les plaquettes CSOI sont collées directement sous vide. Ces plaquettes sont collées avec de l'eau ou un matériau neutre similaire, puis recuites à 1100°C pendant 2 heures maximum pour solidifier la liaison. Après le recuit, il n'y a plus d'adhésif facilitant la liaison entre les plaquettes. Le fait d'effectuer cette opération sous vide permet d'éviter que les cavités ne retiennent un excès d'air ou d'autres contaminants. Cela permet également de maintenir la cohérence lors de l'amincissement de la tranche de silicium, car la pression à l'intérieur des cavités est uniforme sur l'ensemble du substrat.
7. Éclaircir la tranche supérieure (dispositif) avec une gravure CMP/KOH (hydroxyde de potassium).
- La plaquette de couverture doit être amincie jusqu'à l'épaisseur de la couche de dispositif souhaitée. Il s'agit de l'étape la plus variable de la fabrication du CSOI, car la vitesse et la qualité de l'amincissement dépendent fortement de la qualité de la liaison, ainsi que des caractéristiques physiques des cavités. Naturellement, les diaphragmes en silicium vibrent au cours de cette étape, ce qui crée un TTV variable dans ces régions. Le fait d'effectuer les étapes de fabrication précédentes sous vide permet d'éviter bon nombre de ces problèmes.
8. Traitement secondaire, en fonction de l'application et des spécifications de l'appareil
- Contrairement aux plaques SOI plus conventionnelles, les plaques CSOI peuvent subir un traitement secondaire de la face arrière après la fabrication. Cela signifie des membranes extrêmement fines, des structures de surface délicates, des empilements de films métalliques et, d'une manière générale, une plus grande liberté de conception que les plaquettes SOI conventionnelles.
Avantages des plaques de C-SOI :
- Réduit le coût des appareils sans compromettre la précision ou la qualité.
- Réduit la taille de l'appareil. L'inclusion de cavités permet d'obtenir des couches de poignée/BOX/appareil extrêmement fines.
- Le collage de plaquettes à motifs permet un traitement double face de la couche SOI et ouvre de nombreuses possibilités dans le domaine de la micromécanique.
Applications :
Les plaques SOI pré-gravées constituent une plate-forme appropriée pour les structures se déplaçant verticalement et horizontalement dans diverses applications, telles que les capteurs inertiels capacitifs, les capteurs de pression, les microphones et les dispositifs micrsurluidiques.
Bien que la plupart des utilisations se fassent actuellement dans les applications MEMS et capteurs, ces plaquettes peuvent améliorer toute application de plaquette SOI.
Vous ne trouvez pas ce que vous cherchez ?
Si vous avez une question ou souhaitez demander un devis, veuillez contacter un membre de notre équipe de vente.
Contactez nousInventaire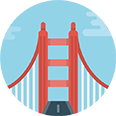
N'importe où dans la région de la Baie dans un délai de 4 heures.
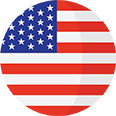
Aux États-Unis dans un délai de 1 jour.
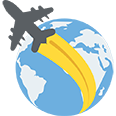
International dans un délai de 3 jours.