Chemische Gasphasenabscheidung
Chemische Gasphasenabscheidung (CVD) ist ein linearer Wachstumsprozess, bei dem ein Vorläufergas eine dünne Schicht auf einem Wafer in einem Reaktor abscheidet. Der Wachstumsprozess findet bei niedrigen Temperaturen statt und hat im Vergleich zu thermischem Oxid eine viel höhere Wachstumsrate. Es erzeugt auch viel dünnere Siliziumdioxidschichten, da der Film abgelagert wird, anstatt zu wachsen. Bei diesem Verfahren entsteht ein Film mit einem hohen elektrischen Widerstand, der sich unter anderem hervorragend für ICs und MEMS-Geräte eignet.
Die chemische Gasphasenabscheidung (CVD) von Oxid wird durchgeführt, wenn eine externe Schicht benötigt wird, das Siliziumsubstrat aber möglicherweise nicht oxidiert werden kann.
Wachstum durch chemische Gasphasenabscheidung:
Beim CVD-Wachstum wird ein Gas oder Dampf (Vorläufer) in einen Niedertemperaturreaktor eingeleitet, in dem die Wafer entweder vertikal oder horizontal angeordnet sind. Das Gas bewegt sich durch das System und verteilt sich gleichmäßig auf der Oberfläche der Wafer. Während sich diese Vorläufer durch den Reaktor bewegen, beginnen die Wafer, sie auf ihrer Oberfläche zu absorbieren.
Sobald sich die Vorläuferstoffe gleichmäßig im System verteilt haben, beginnen chemische Reaktionen auf der Oberfläche der Substrate. Diese chemischen Reaktionen beginnen als Inseln. Im weiteren Verlauf des Prozesses wachsen die Inseln und verschmelzen zu der gewünschten Schicht. Durch die chemischen Reaktionen entstehen auf der Oberfläche der Wafer Nebenprodukte, die durch die Grenzschicht diffundieren und aus dem Reaktor fließen, so dass nur die Wafer mit der aufgebrachten Schicht zurückbleiben.
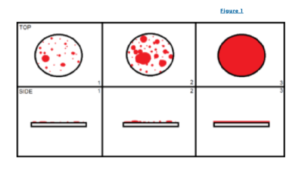
(1.) Gas/Dampf beginnt zu reagieren und bildet Inseln auf der Substratoberfläche. (2.) Die Inseln wachsen und beginnen, miteinander zu verschmelzen. (3.) Es entsteht ein kontinuierlicher, gleichmäßiger Film.
Vorteile der chemischen Gasphasenabscheidung:
- Wachstumsprozess bei niedriger Temperatur.
- Schnelle Abscheidungsrate (insbesondere APCVD).
- Es muss nicht unbedingt ein Siliziumsubstrat sein.
- Gute Stufenabdeckung (insbesondere PECVD).
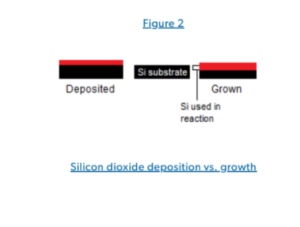
Arten von CVD
LPCVD
Die chemische Gasphasenabscheidung bei niedrigem Druck ist ein Standardverfahren der chemischen Gasphasenabscheidung ohne Druckbeaufschlagung. Der Hauptunterschied zwischen LPCVD und anderen CVD-Verfahren ist die Abscheidungstemperatur. Bei der LPCVD wird die höchste Temperatur für die Abscheidung von Schichten verwendet, typischerweise über 600°C.
Die Niederdruckumgebung erzeugt einen sehr gleichmäßigen Film mit hoher Reinheit, Reproduzierbarkeit und Homogenität. Dies geschieht zwischen 10 - 1.000 Pa, während der Standarddruck im Raum 101.325 Pa beträgt. Die Temperatur bestimmt die Dicke und Reinheit dieser Filme, wobei höhere Temperaturen zu dickeren und reineren Filmen führen.
PECVD
Die plasmaunterstützte chemische Gasphasenabscheidung ist ein Verfahren zur Abscheidung von Schichten mit hoher Dichte bei niedriger Temperatur. PECVD findet in einem CVD-Reaktor unter Zugabe von Plasma statt, einem teilweise ionisierten Gas mit einem hohen Gehalt an freien Elektronen (~50 %). Es handelt sich um ein Niedertemperatur-Abscheidungsverfahren, das zwischen 100°C und 400°C stattfindet. PECVD kann bei niedrigen Temperaturen durchgeführt werden, da die Energie der freien Elektronen die reaktiven Gase dissoziiert und einen Film auf der Waferoberfläche bildet.
Bei dieser Beschichtungsmethode werden zwei verschiedene Plasmatypen verwendet:
- Kalt (nicht thermisch): Elektronen haben eine höhere Temperatur als die neutralen Teilchen und Ionen. Bei dieser Methode wird die Energie der Elektronen genutzt, indem der Druck in der Abscheidungskammer verändert wird.
- Thermisch: Die Elektronen haben die gleiche Temperatur wie die Partikel und Ionen in der Beschichtungskammer.
In der Abscheidekammer wird eine Hochfrequenzspannung zwischen Elektroden über und unter dem Wafer gesendet. Dadurch werden die Elektronen aufgeladen und in einem erregbaren Zustand gehalten, um den gewünschten Film abzuscheiden.
Das Wachstum von Schichten mittels PECVD erfolgt in vier Schritten:
- Target-Wafer auf eine Elektrode in der Beschichtungskammer legen.
- Reaktive Gase und Abscheidungselemente in die Kammer einführen.
- Plasma zwischen Elektroden schicken und Spannung anlegen, um das Plasma anzuregen.
- Reaktives Gas dissoziiert und reagiert mit der Waferoberfläche, um einen dünnen Film zu bilden. Die Nebenprodukte diffundieren aus der Kammer.
APCVD
Die chemische Gasphasenabscheidung bei Atmosphärendruck ist ein Niedertemperaturverfahren, das in einem Ofen bei normalem Atmosphärendruck durchgeführt wird. Wie bei anderen CVD-Verfahren wird auch bei der APCVD ein Vorläufergas in der Beschichtungskammer benötigt, dann steigt die Temperatur langsam an, um die Reaktionen auf der Waferoberfläche zu katalysieren und eine dünne Schicht abzuscheiden. Aufgrund der Einfachheit dieses Verfahrens ist die Abscheidungsrate sehr hoch.
- Häufig abgeschiedene Schichten: dotierte und undotierte Siliziumoxide, Siliziumnitride. Wird auch beim Glühen verwendet.
HDP CVD
Die plasmachemische Gasphasenabscheidung mit hoher Dichte ist eine Variante der PECVD, bei der ein Plasma mit höherer Dichte verwendet wird, so dass die Wafer mit einer noch niedrigeren Temperatur (zwischen 80°C und 150°C) in der Abscheidungskammer reagieren können. Dadurch entsteht auch ein Film, der sich hervorragend zum Füllen von Gräben eignet.
- Häufig abgeschiedene Schichten: Siliziumdioxid (SiO2), Siliziumnitrid (Si3N4), Siliziumkarbid (SiC).
SACVD
Die chemische Gasphasenabscheidung bei subatmosphärischem Druck unterscheidet sich von anderen Methoden, da sie unterhalb des normalen Raumdrucks stattfindet und Ozon (O3) als Katalysator für die Reaktion verwendet wird. Der Abscheidungsprozess findet bei einem höheren Druck als LPCVD, aber niedriger als APCVD statt, nämlich zwischen etwa 13.300 Pa und 80.000 Pa. SACVD-Filme haben eine hohe Abscheidungsrate, die sich mit steigender Temperatur bis etwa 490°C verbessert und dann abnimmt.
- Gemeinsame Filme hinterlegt: BPSG, PSG, TEOS.
USG, BPSG
Undotiertes Silikatglas - USG
Undotiertes Silikatglas hat eine hohe Abscheidungsrate bei niedrigen Temperaturen und weist ähnliche Eigenschaften wie Siliziumdioxid auf. Das bedeutet, dass es sich leicht mittels plasmaunterstützter CVD (PECVD), HDP-CVD oder SACVD abscheiden lässt. Es wird am häufigsten als Isolator und Passivierungsschicht in Multilevel-IMD-Anwendungen verwendet.
Borophosphosilikatglas - BPSG
Borphosphosilikatglas (BPSG) ist eine Beschichtung aus einer Mischung von Sauerstoff und Hydriden von Silizium (Silan - SiH4), Bor (Diboran - B2H6) und Phosphor (Phosphin - PH3). Es wird auch als dotierte Oxidschicht bezeichnet, da es ähnlich wieSiliziumdioxidist, dem Bor und Phosphor hinzugefügt wurden, die seine thermischen Eigenschaften verändern. Durch die Zugabe von Hydriden wird der Schmelzpunkt von Glas drastisch gesenkt, was dieses Verfahren sehr nützlich macht, wenn ein Wafer nur begrenzte thermische Fähigkeiten hat.
BPSG wird mit verschiedenen Techniken der chemischen Gasphasenabscheidung (CVD) auf Wafer aufgebracht. Die effektivste und gebräuchlichste Abscheidungstechnik ist PECVD, obwohl auch andere CVD-Verfahren funktionieren. Atmosphärendruck-CVD (APCVD), Subatmosphärendruck-CVD (SACVD), Niederdruck-CVD (LPCVD) und Hochdichte-Plasma-CVD (HDP-CVD) sind einige der anderen CVD-Verfahren, mit denen BPSG auf einen Wafer aufgebracht werden kann.
Das Verhältnis von Sauerstoff zu Hydriden in der Abscheidekammer liegt in der Regel zwischen 40:1 und 60:1, was die Abscheidetemperatur von BPSG im Vergleich zu anderen dotierten Oxidschichten deutlich senkt. Für die Abscheidung dieser Schichten beträgt die Ofentemperatur 360°C - 390°C, wobei die optimale Abscheidungstemperatur bei etwa 370°C liegt.
Um sicherzustellen, dass diese Wafer die intermetallischen Dielektrika ordnungsgemäß isolieren und ihre hohe Ebenheit beibehalten, werden diese Wafer häufig einem Reflow-Prozess unterzogen, der entweder in einem Ofen oder durch schnelles thermisches Ausglühen (RTA) erfolgt. Aufgrund ihrer Temperaturempfindlichkeit werden diese Wafer keinen Temperaturen über 900°C ausgesetzt, um Schäden und Unvollkommenheiten zu vermeiden. Das bedeutet auch, dass die RTA bei einer niedrigeren Temperatur durchgeführt wird.
Borophosphosilikatglas schützt das darunter liegende Siliziumsubstrat und die Leiterbahnen in Halbleitern und hilft bei der Planarisierung von Geräten. Dies macht BPSG besonders wertvoll bei der Herstellung von Halbleiterbauelementen, intermetallischen Dielektrika (IMD) und prämetallischen Dielektrika (PMD).