Was ist ein Silizium-Wafer?
Silizium ist ein graues, sprödes, vierwertiges, chemisches Element. Es macht 27,8% der Erdkruste aus und ist neben Sauerstoff das am häufigsten vorkommende Element in der Natur. Einige der häufigsten Materialien, die Silizium enthalten, sind unter anderem Quarz, Achat, Feuerstein und gewöhnlicher Strandsand. Es ist der Hauptbestandteil von Baumaterialien wie Zement, Ziegel und Glas. Silizium ist auch das gängigste Material für die Herstellung von Halbleitern und Mikrochips. Ironischerweise leitet Silizium selbst Elektrizität nicht sehr gut. Es kann jedoch Dotierstoffe aufnehmen, um den spezifischen Widerstand genau zu steuern.
Bevor ein Halbleiter hergestellt werden kann, muss sich Silizium in einen Wafer verwandeln, der zu einem Silizium-Wafer wird. Dies beginnt mit dem Wachstum eines Siliziumblocks. Ein Silizium-Einkristall besteht aus Atomen, die in einem dreidimensionalen periodischen Muster angeordnet sind, das sich durch das gesamte Material zieht. A Poly-Silizium Kristall besteht aus vielen kleinen Einkristallen mit unterschiedlichen Ausrichtungen, die allein nicht für Halbleiterbauelemente verwendet werden können.
Herstellung von Silizium-Wafern
Die Zeit, die für die Züchtung eines Siliziumblocks benötigt wird, hängt von vielen Faktoren ab. Mehr als 75% aller einkristallinen Silizium-Wafer werden nach der Czochralski (CZ)-Methode hergestellt. Für die CZ-Züchtung von Barren werden Stücke von unbearbeitetem polykristallinem Silizium benötigt. Diese Brocken werden zusammen mit kleinen Mengen bestimmter Elemente der Gruppen III und V, den so genannten Dotierstoffen, in einen Quarztiegel gegeben. Die hinzugefügten Dotierstoffe verleihen dem gezüchteten Barren die gewünschten elektrischen Eigenschaften. Die gängigsten Dotierstoffe sind Bor, Phosphor, Arsen und Antimon. Je nach Dotierstoff wird der Barren zu einem P- oder N-Typ (Bor: P-Typ; Phosphor, Antimon, Arsen: N-Typ).
Wachstum der Barren
Um einen Barren zu züchten, wird das Silizium zunächst auf 1420°C erhitzt, also über den Schmelzpunkt von Silizium. Sobald die Kombination aus polykristallinem Material und Dotierstoff verflüssigt ist, wird ein einzelner Siliziumkristall, der Keim, auf der Schmelze positioniert und berührt die Oberfläche kaum. Der Keim hat die gleiche Kristallorientierung wie der fertige Barren. Um eine gleichmäßige Dotierung zu erreichen, rotieren der Impfkristall und der Tiegel mit geschmolzenem Silizium in entgegengesetzte Richtungen. Sobald das System die richtigen Bedingungen für das Kristallwachstum erreicht hat, hebt sich der Impfkristall langsam aus der Schmelze. Das Wachstum beginnt mit einem schnellen Ziehen des Keimkristalls. Dadurch wird die Anzahl der Kristalldefekte im Impfkristall zu Beginn des Wachstumsprozesses minimiert.
Danach wird die Ziehgeschwindigkeit reduziert, damit der Durchmesser des Kristalls zunimmt. Wenn der gewünschte Durchmesser erreicht ist, werden die Wachstumsbedingungen stabilisiert, um den Durchmesser beizubehalten. Wenn der Keim langsam über die Schmelze gehoben wird, bewirkt die Oberflächenspannung zwischen dem Keim und der Schmelze, dass ein dünner Film des Siliziums am Keim haftet und dann abkühlt. Beim Abkühlen orientieren sich die Atome im geschmolzenen Silizium an der Kristallstruktur des Keims.
Schneiden
Sobald der Ingot ausgewachsen ist, wird er auf einen groben Durchmesser geschliffen, der etwas größer ist als der Zieldurchmesser des endgültigen Silizium-Wafer. In den Ingot wird eine Kerbe oder eine Abflachung geschnitten, um seine Ausrichtung zu kennzeichnen. Nachdem er eine Reihe von Kontrollen bestanden hat, wird der Ingot in Scheiben geschnitten. Aufgrund der Härte des Siliziums werden die Siliziumscheiben mit einer Diamantsäge sorgfältig geschnitten, so dass sie etwas dicker sind als die Zielvorgaben. Die Diamantsäge trägt auch dazu bei, Schäden an den Wafern, Dickenschwankungen sowie Verformungen und Verwerfungen zu minimieren.
Nachdem die Wafer in Scheiben geschnitten wurden, beginnt der Läppprozess. Durch das Läppen des Wafer werden Sägemarken und Oberflächendefekte auf der Vorder- und Rückseite des Wafer entfernt. Außerdem wird der Wafer dadurch dünner und die Spannungen, die sich durch das Schneiden im Wafer angesammelt haben, werden abgebaut. Nach dem Läppen der Silizium-Wafer werden diese einem Ätz- und Reinigungsprozess unterzogen. Natriumhydroxid oder Essig- und Salpetersäure beseitigen mikroskopische Risse und/oder Oberflächenbeschädigungen, die beim Läppen entstanden sein könnten. Ein kritisches Kantenschleifverfahren wird durchgeführt, um die Kanten abzurunden und so die Wahrscheinlichkeit eines Bruchs in den verbleibenden Fertigungsschritten und später bei der Verwendung der Wafer durch die Gerätehersteller drastisch zu verringern.
Nach dem Abrunden der Kanten werden diese, je nach Spezifikation des Endverbrauchers, oft noch zusätzlich poliert, um die allgemeine Sauberkeit zu verbessern und die Bruchgefahr um bis zu 400% zu verringern.
Reinigung
Der letzte und wichtigste Schritt im Herstellungsprozess ist das Polieren des Wafers. Dieser Prozess findet in einem Reinraum statt. Reinräume haben ein Bewertungssystem, das von Klasse 1 bis Klasse 10.000 reicht. Die Einstufung entspricht der Anzahl der Partikel pro Kubikfuß. Diese Partikel sind mit dem bloßen Auge nicht sichtbar. In einer unkontrollierten Atmosphäre, wie z.B. in einem Wohnzimmer oder Büro, würde die Partikelanzahl wahrscheinlich 5 Millionen pro Kubikfuß betragen. Um diesen Reinheitsgrad aufrechtzuerhalten, müssen die Arbeiter Reinraumanzüge tragen, die ihren Körper von Kopf bis Fuß bedecken und in denen sich keine Partikel ansammeln oder übertragen können. Außerdem stehen sie unter einem Ventilator, der alle kleinen Partikel wegbläst, die sich vor dem Betreten des Raums angesammelt haben könnten.
Politur
Die meisten erstklassigen Silizium-Wafer durchlaufen 2-3 Stufen des Polierens, wobei immer feinere Schlämme oder Poliermittel verwendet werden. Meistens werden die Wafer nur auf der Vorderseite poliert, mit Ausnahme von 300-mm-Wafern, die beidseitig poliert werden. Durch das Polieren wird eine Hochglanzoberfläche erzeugt. Durch das Polieren wird auch festgelegt, welche Seite für die Herstellung der Geräte verwendet wird. Diese Oberfläche muss frei von Topographie, Mikrorissen, Kratzern und Restbeschädigungen sein.
Der Polierprozess erfolgt in zwei Schritten, nämlich dem Abtragen des Materials und dem abschließenden chemisch-mechanischen Polieren (CMP). Bei beiden Prozessen werden Polierpads und Polierschlämme verwendet. Beim Abtragen des Materials wird eine sehr dünne Siliziumschicht entfernt, die notwendig ist, um die Oberfläche des Wafer nicht zu beschädigen. Bei der abschließenden Politur hingegen wird kein Material entfernt. Während des Abtrags bildet sich ein Schleier auf der Oberfläche des Wafer, so dass ein zusätzlicher Polierschritt den Wafer auf Hochglanz bringt.
Nach dem Polieren durchlaufen die Silizium-Wafer eine abschließende Reinigungsphase, bei der eine lange Reihe von Reinigungsbädern verwendet wird. Bei diesem Prozess werden Oberflächenpartikel, Spuren von Metallen und Rückstände entfernt. Häufig wird auch die Rückseite gereinigt, um selbst die kleinsten Partikel zu entfernen.
Verpackung
Sobald die Silizium-Wafer den letzten Reinigungsschritt durchlaufen haben, werden sie von den Ingenieuren nach Spezifikationen sortiert und unter Hochintensitätslicht oder mit Laserscannern untersucht. Dadurch werden unerwünschte Partikel oder andere Defekte aufgespürt, die während der Herstellung entstanden sein könnten. Alle Silizium-Wafer, die die richtigen Spezifikationen erfüllen, werden in Kassetten verpackt und mit Klebeband versiegelt. Die Silizium-Wafer werden in einem vakuumversiegelten Plastikbeutel mit einer luftdichten Schichthülle versandt. Dadurch wird sichergestellt, dass beim Verlassen des Reinraums keine Partikel oder Feuchtigkeit in die Kassette gelangen.
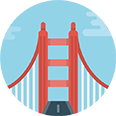
Überall in der Bay Area innerhalb von 4 Stunden.
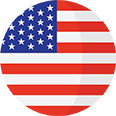
In den Vereinigten Staaten innerhalb von 1 Tag.
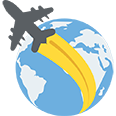
International innerhalb von 3 Tagen.