Qu'est-ce qu'une plaquette de silicium ?
Le silicium est un élément chimique gris, fragile et tétravalent. Il constitue 27,8 % de la croûte terrestre et, après l'oxygène, c'est l'élément le plus abondant dans la nature. Le quartz, l'agate, le silex et le sable de plage sont parmi les matériaux les plus courants qui contiennent du silicium. Le silicium est le principal composant des matériaux de construction tels que le ciment, la brique et le verre. Le silicium est également le matériau le plus courant pour fabriquer des semi-conducteurs et des micropuces. Paradoxalement, le silicium en lui-même ne conduit pas très bien l'électricité ; cependant, il peut recevoir des dopants de manière précise afin de contrôler la résistivité selon une spécification exacte.
Avant qu'un semi-conducteur puisse être fabriqué, le silicium doit être transformé en une plaquette qui devient une plaquette de silicium. Cela commence par la croissance d'un lingot de silicium. Un cristal de silicium unique est constitué d'atomes disposés selon un schéma périodique tridimensionnel qui s'étend à l'ensemble du matériau. A polysilicium est formé d'un grand nombre de petits cristaux uniques ayant des orientations différentes qui, seuls, ne peuvent pas être utilisés pour des dispositifs semi-conducteurs.
Fabrication de plaquettes de silicium
Le temps nécessaire à la croissance d'un lingot de silicium varie en fonction de nombreux facteurs. Plus de 75 % des plaquettes de silicium monocristallin sont produites selon la méthode Czochralski (CZ). La croissance des lingots CZ nécessite des morceaux de silicium polycristallin vierge. Ces morceaux sont placés dans un creuset en quartz avec de petites quantités d'éléments spécifiques du groupe III et du groupe V appelés dopants. Les dopants ajoutés confèrent les propriétés électriques souhaitées au lingot cultivé. Les dopants les plus courants sont le bore, le phosphore, l'arsenic et l'antimoine. Selon le dopant, le lingot devient un lingot de type P ou N (bore : type P ; phosphore, antimoine, arsenic : type N).
Croissance des lingots
Pour produire un lingot, la première étape consiste à chauffer le silicium à 1420°C, au-dessus du point de fusion du silicium. Une fois que la combinaison polycristalline et dopante a été liquéfiée, un cristal de silicium unique, le germe, est placé au-dessus de la masse fondue, en touchant à peine la surface. Le germe a la même orientation cristalline que celle requise dans le lingot fini. Pour assurer l'uniformité du dopage, le cristal de semence et le creuset de silicium en fusion tournent dans des directions opposées. Une fois que le système a atteint les conditions nécessaires à la croissance des cristaux, le cristal de semence se détache lentement de la matière en fusion. La croissance commence par une traction rapide du cristal de semence. Cela permet de minimiser le nombre de défauts cristallins dans le germe au début du processus de croissance.
Ensuite, la vitesse de traction diminue pour permettre au diamètre du cristal d'augmenter. Lorsque le diamètre souhaité est obtenu, les conditions de croissance sont stabilisées pour maintenir le diamètre. Lorsque le germe est lentement soulevé au-dessus de la matière fondue, la tension superficielle entre le germe et la matière fondue fait qu'une fine pellicule de silicium adhère au germe et se refroidit. Pendant le refroidissement, les atomes du silicium fondu s'orientent vers la structure cristalline de la graine.
Trancher
Une fois que le lingot est entièrement cultivé, il est broyé pour obtenir un diamètre approximatif légèrement supérieur au diamètre cible de la plaquette de silicium finale. Le lingot est entaillé ou aplati afin d'indiquer son orientation. Après avoir subi un certain nombre d'inspections, le lingot est découpé en tranches. En raison de la dureté du silicium, une scie diamantée tranche soigneusement les plaquettes de silicium de manière à ce qu'elles soient légèrement plus épaisses que la spécification visée. La scie diamantée permet également de minimiser les dommages causés aux plaquettes, les variations d'épaisseur et les défauts de courbure et de gauchissement.
Une fois les tranches tranchées, le processus de rodage commence. Le rodage élimine les marques de scie et les défauts de surface sur les faces avant et arrière de la plaquette. Il permet également d'amincir la plaquette et d'atténuer les tensions accumulées dans la plaquette lors du processus de tranchage. Après le rodage, les plaquettes de silicium sont soumises à un processus de gravure et de nettoyage. L'hydroxyde de sodium ou les acides acétique et nitrique éliminent les fissures microscopiques et/ou les dommages de surface qui ont pu se produire pendant le rodage. Une procédure de meulage des bords critiques permet d'arrondir les bords, ce qui réduit considérablement la probabilité de rupture au cours des étapes suivantes de la fabrication et, plus tard, lorsque les fabricants d'appareils utiliseront les plaquettes.
Après avoir arrondi les bords, selon les spécifications de l'utilisateur final, les bords sont souvent soumis à une étape de polissage supplémentaire, ce qui améliore la propreté générale et réduit encore la casse jusqu'à 400 %.
Nettoyage
L'étape finale et la plus cruciale du processus de fabrication est le polissage de la plaquette. Ce processus se déroule dans une salle blanche. Les salles blanches ont un système de classification qui va de la classe 1 à la classe 10 000. La classification correspond au nombre de particules par mètre cube. Ces particules ne sont pas visibles à l'œil nu et dans une atmosphère non contrôlée, comme celle d'un salon ou d'un bureau, le nombre de particules serait probablement de 5 millions par mètre cube. Pour maintenir ce niveau de propreté, les travailleurs doivent porter des combinaisons de salle blanche qui couvrent leur corps de la tête aux pieds et ne recueillent ni ne transportent aucune particule. Ils se tiennent également sous un ventilateur qui souffle les petites particules qui auraient pu s'accumuler avant d'entrer dans la pièce.
Polissage
La plupart des plaquettes de silicium de première qualité passent par deux ou trois étapes de polissage, en utilisant des boues ou des composés de polissage de plus en plus fins. La plupart du temps, les plaquettes sont polies sur la face avant uniquement, à l'exception des plaquettes de 300 mm qui sont polies sur les deux faces. Le polissage permet d'obtenir une finition miroir. Le polissage permet également de distinguer la face à utiliser pour la fabrication du dispositif. Cette surface doit être exempte de topographie, de micrsurissures, de rayures et de dommages résiduels dus au travail.
Le processus de polissage se déroule en deux étapes, à savoir l'enlèvement de la matière et le polissage mécanique chimique final (CMP). Les deux processus utilisent des tampons de polissage et de la boue de polissage. Le processus d'enlèvement du stock élimine une très fine couche de silicium et est nécessaire pour produire une surface de plaquette sans dommages. En revanche, le polissage final n'enlève aucun matériau. Pendant le processus d'enlèvement de la matière, un voile se forme à la surface de la plaquette, de sorte qu'une étape de polissage supplémentaire donne à la plaquette une finition miroir.
Après le polissage, les plaquettes de silicium passent par une étape de nettoyage final qui utilise une longue série de bains propres. Ce processus permet d'éliminer les particules de surface, les traces de métaux et les résidus. Souvent, un lavage de la face arrière est effectué pour éliminer les plus petites particules.
Emballage
Une fois que les plaquettes de silicium ont franchi l'étape finale du nettoyage, les ingénieurs les trient en fonction de leurs spécifications et les inspectent sous des lumières à haute intensité ou des systèmes de balayage laser. Ils détectent ainsi les particules indésirables ou d'autres défauts susceptibles d'être apparus au cours de la fabrication. Toutes les plaquettes de silicium qui répondent aux spécifications appropriées sont emballées dans des cassettes et scellées avec du ruban adhésif. Les plaquettes de silicium sont expédiées dans un sac en plastique scellé sous vide avec un sac extérieur en aluminium étanche à l'air. Cela garantit qu'aucune particule ou humidité ne pénètre dans la cassette à la sortie de la salle blanche.
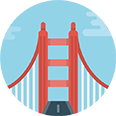
N'importe où dans la région de la Baie dans un délai de 4 heures.
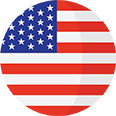
Aux États-Unis dans un délai de 1 jour.
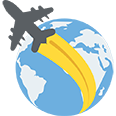
International dans un délai de 3 jours.