실리콘 웨이퍼란?
실리콘은 회색의 부서지기 쉬운 4가 화학 원소입니다. 지각의 27.8%를 구성하며 산소 다음으로 자연에서 가장 풍부한 원소입니다. 실리콘을 함유한 가장 일반적인 재료로는 석영, 마노, 부싯돌, 일반적인 해변 모래 등이 있습니다. 실리콘은 시멘트, 벽돌, 유리와 같은 건축 자재의 주요 구성 요소입니다. 또한 실리콘은 반도체와 마이크로칩을 만드는 데 가장 많이 사용되는 재료이기도 합니다. 아이러니하게도 실리콘은 그 자체로는 전기를 잘 전도하지 않지만, 도펀트를 첨가하면 저항을 정확한 사양으로 제어할 수 있습니다.
반도체를 만들기 위해서는 실리콘이 웨이퍼가 되어 실리콘 웨이퍼가 되어야 합니다. 이는 실리콘 잉곳의 성장으로 시작됩니다. 단결정 실리콘은 물질 전체에 걸쳐 3차원 주기적 패턴으로 배열된 원자로 구성됩니다. 폴리실리콘 결정은 방향이 다른 여러 개의 작은 단결정으로 형성되며, 이 결정만으로는 반도체 장치에 사용할 수 없습니다.
실리콘 웨이퍼 제조
실리콘 잉곳을 성장시키는 데 걸리는 시간은 여러 요인에 따라 달라집니다. 전체 단결정 실리콘 웨이퍼의 75% 이상이 쵸크랄스키(Czochralski, CZ) 방법을 통해 성장합니다. CZ 잉곳 성장에는 순수 다결정 실리콘 덩어리가 필요합니다. 이러한 덩어리는 도펀트라고 하는 소량의 특정 그룹 III 및 그룹 V 원소와 함께 석영 도가니에 배치됩니다. 추가된 도펀트는 성장한 잉곳에 원하는 전기적 특성을 부여합니다. 가장 일반적인 도펀트는 붕소, 인, 비소 및 안티몬입니다. 도펀트에 따라 잉곳은 P형 또는 N형 잉곳이 됩니다 (붕소: P형; 인, 안티몬, 비소: N형).
잉곳 성장
잉곳을 성장시키기 위한 첫 번째 단계는 실리콘의 융점보다 높은 1420°C로 실리콘을 가열하는 것입니다. 다결정과 도펀트 조합이 액화되면 단일 실리콘 결정인 시드가 용융물 표면위에 거의 닿지 않게 배치됩니다. 이 시드는 완성된 잉곳에 필요한 것과 동일한 결정 방향을 갖습니다. 도핑 균일성을 달성하기 위해 시드 결정과 용융 실리콘의 도가니는 반대 방향으로 회전합니다. 시스템이 결정 성장을 위한 적절한 조건에 도달하면 시드 결정이 용융물에서 천천히 들어 올려집니다. 성장은 시드 결정이 빠르게 당겨지면서 시작됩니다. 이는 성장 과정 초기에 시드 내 결정 결함의 수를 최소화합니다.
그 후 당기는 속도가 감소하여 결정의 직경이 증가합니다. 원하는 직경이 얻어지면 성장 조건이 안정화되어 직경이 유지됩니다. 시드를 용융물 위로 천천히 들어 올리면 시드와 용융물 사이의 표면 장력으로 인해 실리콘의 얇은 막이 시드에 부착된 후 냉각됩니다. 냉각되는 동안 녹은 실리콘의 원자는 시드의 결정 구조에 따라 방향을 잡습니다.
슬라이싱
잉곳이 완전히 성장하면 최종 실리콘 웨이퍼의 목표 직경보다 약간 큰 대략적인 크기의 직경으로 연마됩니다. 잉곳에는 방향을 표시하기 위해 노치 또는 플랫 절단면이 있습니다. 여러 검사를 통과한 후 잉곳은 슬라이싱을 진행합니다. 실리콘의 경도 때문에 다이아몬드 엣지 톱은 실리콘 웨이퍼를 목표 사양보다 약간 두껍게 조심스럽게 슬라이스합니다. 다이아몬드 엣지 톱은 웨이퍼의 손상, 두께 변화, 보우 및 워프 결함을 최소화하는 데도 도움이 됩니다.
웨이퍼가 슬라이스된 후 래핑(lapping) 공정이 시작됩니다. 웨이퍼를 래핑하면 웨이퍼의 앞면과 뒷면에서 톱 자국과 표면 결함이 제거됩니다. 또한 웨이퍼를 얇게 만들고 슬라이싱 공정에서 웨이퍼에 축적된 스트레스를 완화하는 데 도움이 됩니다. 실리콘 웨이퍼를 래핑한 후에는 에칭 및 세정 공정을 거칩니다. 수산화나트륨 또는 아세트산과 질산은 래핑 과정에서 발생할 수 있는 미세한 균열 및/또는 표면 손상을 완화합니다. 가장자리를 둥글게 만드는 중요한 에지 연마 공정이 진행되어 나머지 제조 단계와 이후 디바이스 제조업체에서 웨이퍼를 사용할 때 파손될 확률을 크게 줄입니다.
최종 사용자의 사양에 따라 모서리를 둥글게 다듬은 후 추가 연마 단계를 거쳐 전체적인 청결도를 개선하고 파손을 최대 400%까지 줄이는 경우가 많습니다.
세정 (클리닝)
제조 공정의 마지막이자 가장 중요한 단계는 웨이퍼를 연마하는 것입니다. 이 공정은 클린룸에서 이루어집니다. 클린룸은 클래스1부터 클래스10,000까지 등급 시스템이 있습니다. 등급은 입방 피트당 입자 수에 해당합니다. 이러한 입자는 육안으로 보이지 않으며 거실이나 사무실과 같이 통제되지 않은 환경에서는 입방 피트당 입자 수가 5백만 개가 될 수 있습니다. 이러한 수준의 청결을 유지하기 위해 작업자는 머리부터 발끝까지 몸을 덮고 입자를 모으거나 운반하지 않는 클린룸 슈트를 착용해야 합니다. 또한 작업자는 선풍기 아래에 서서 실내에 들어가기 전에 쌓여 있을 수 있는 작은 입자를 모두 날려버립니다.
연마
대부분의 프라임 등급 실리콘 웨이퍼는 점점 더 미세한 슬러리 또는 폴리싱 컴파운드를 사용하여 2~3단계의 연마 과정을 거칩니다. 양면 연마되는 300mm 웨이퍼를 제외하고는 대부분의 경우 웨이퍼는 앞면만 연마됩니다. 폴리싱/연마는 거울 마감을 만들어냅니다. 또한 폴리싱은 디바이스 제작에 사용할 면을 구분합니다. 이 표면에는 지형, 미세 균열, 긁힘 및 잔여 작업 손상이 없어야 합니다.
연마 공정은 스톡 제거와 최종 화학적 기계적 연마(CMP)의 두 단계로 진행됩니다. 두 공정 모두 폴리싱 패드와 폴리싱 슬러리를 사용합니다. 스톡 제거 공정은 매우 얇은 실리콘 층을 제거하며 손상 없는 웨이퍼 표면을 생성하는 데 필요합니다. 반면에 최종 연마에서는 어떤 물질도 제거하지 않습니다. 스톡 제거 공정 중에 웨이퍼 표면에 헤이즈가 형성되므로 추가 연마 단계를 통해 웨이퍼에 거울 마감이 제공됩니다.
폴리싱 후 실리콘 웨이퍼는 일련의 긴 세척조를 사용하는 최종 세척 단계로 진행됩니다. 이 공정에서는 표면 입자, 미량 금속 및 잔류물을 제거합니다. 아주 작은 입자까지 제거하기 위해 종종 뒷면 스크럽을 수행합니다.
포장
실리콘 웨이퍼가 최종 세척 단계를 완료하면 엔지니어가 사양별로 분류하고 고강도 조명 또는 레이저 스캐닝 시스템으로 검사합니다. 이를 통해 제조 과정에서 발생했을 수 있는 원치 않는 입자나 기타 결함을 감지합니다. 적절한 사양을 충족하는 모든 실리콘 웨이퍼는 카세트에 포장되고 테이프로 밀봉됩니다. 실리콘 웨이퍼는 밀폐된 호일 외부 백이 있는 진공 밀봉 비닐 백에 담겨 배송됩니다. 이는 클린룸을 떠날 때 카세트에 입자나 습기가 들어가는 것을 방지합니다.
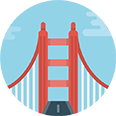
베이 지역 (Bay Area) 어디든 4시간 이내.
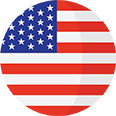
미국에서는 1일 이내.
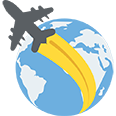
국제적으로 3일 이내.