The History of Silicon Wafer: Evolution of a Technological Marvel
The silicon wafer is an essential component of modern electronics, serving as the foundation for integrated circuits and semiconductor devices. However, the journey of the silicon wafer has been a fascinating progression from early discoveries in materials science to the sophisticated manufacturing processes of today. This page delves into the history of the silicon wafer, exploring its origins, technological breakthroughs, and its pivotal role in shaping the modern world.
The Early Days of Semiconductors
The story of the silicon wafer begins with the discovery of semiconductors in the 19th century. Semiconductors are materials that have electrical conductivity between that of a conductor and an insulator. Silicon, abundant in the Earth’s crust, quickly became a material of interest due to its unique properties.
1824: The Discovery of Silicon
In 1824, Swedish chemist Jöns Jacob Berzelius successfully isolated silicon, laying the groundwork for future applications. While silicon’s electrical properties were not immediately recognized, this discovery marked the first step toward the development of the silicon wafer.
1874: The Semiconductor Effect
German physicist Karl Ferdinand Braun identified the rectifying properties of certain materials, including silicon. This phenomenon, later called the semiconductor effect, demonstrated that materials like silicon could control electrical currents—a critical property for electronics.
The Birth of the Silicon Wafer
While silicon’s potential as a semiconductor material was recognized in the late 19th and early 20th centuries, it wasn’t until the mid-20th century that the silicon wafer emerged as a critical component in electronics.
1947: The Invention of the Transistor
The invention of the transistor at Bell Labs in 1947 by John Bardeen, Walter Brattain, and William Shockley marked a turning point in electronics. The transistor, initially made from germanium, demonstrated the need for a reliable and scalable semiconductor material. Scientists soon turned to silicon as a superior alternative due to its abundance, thermal stability, and ease of doping.
1950s: The Silicon Revolution
The 1950s saw significant advancements in the production of pure silicon crystals, a necessary step for creating the silicon wafer. Techniques like the Czochralski process, developed by Jan Czochralski in 1916 and later adapted for silicon, enabled the growth of single-crystal silicon ingots. These ingots could then be sliced into thin wafers, setting the stage for mass production.
The Evolution of Silicon Wafer Manufacturing
The development of the silicon wafer has been closely tied to advancements in semiconductor fabrication. Each innovation in wafer production has contributed to the rapid progress of electronic devices.
1960s: Integrated Circuits and the Rise of Silicon Wafers
In 1958, Jack Kilby at Texas Instruments and Robert Noyce at Fairchild Semiconductor independently invented the integrated circuit (IC). The IC’s design required a stable and uniform substrate, and the silicon wafer quickly became the industry standard.
By the 1960s, silicon wafers were produced using refined techniques that ensured their purity and flatness. These improvements allowed for the fabrication of more reliable and efficient transistors, diodes, and other components.
1970s: Scaling Down and Improving Quality
As the demand for smaller and more powerful devices grew, so did the need for advanced silicon wafer technology. The 1970s introduced chemical-mechanical polishing (CMP), which created smoother wafer surfaces. This innovation was critical for producing denser integrated circuits with smaller features.
Silicon Wafer in the Era of Microprocessors
The introduction of the microprocessor in the 1970s marked a new era for silicon wafers. Companies like Intel and AMD relied on high-quality silicon wafers to produce processors that revolutionized computing.
The 4004 Microprocessor
Intel’s 4004, released in 1971, was the first commercially available microprocessor. Built on a silicon wafer, it contained over 2,000 transistors and operated at a clock speed of 740 kHz. This achievement demonstrated the potential of silicon wafers to enable complex electronic systems.
Advancements in Wafer Sizes
During this period, the industry began producing larger silicon wafers to meet the increasing demand for integrated circuits. Moving from 2-inch to 4-inch wafers allowed manufacturers to fit more chips on each wafer, improving efficiency and reducing costs.
Modern Silicon Wafer Technology
Today, the silicon wafer is at the heart of the semiconductor industry, supporting the development of advanced technologies like artificial intelligence (AI), 5G, and renewable energy solutions. The evolution of silicon wafer technology reflects the relentless pursuit of innovation in materials science and electronics.
Larger Wafer Sizes
The industry has continued to increase wafer sizes over the decades. Standard wafer sizes have grown from 6 inches in the 1980s to 8 inches in the 1990s and 12 inches (300 mm) in the 2000s. Larger wafers allow manufacturers to produce more chips per wafer, driving down costs and increasing production efficiency.
Improved Purity and Doping Techniques
Modern silicon wafers are manufactured with incredibly high purity levels, often exceeding 99.9999999% (referred to as “9N” purity). Advanced doping techniques ensure precise control over the electrical properties of the wafer, enabling the production of high-performance semiconductors.
Silicon-On-Insulator (SOI) Wafers
SOI wafers, introduced in the late 20th century, are a specialized type of silicon wafer with an insulating layer. These wafers improve the performance and energy efficiency of integrated circuits, making them ideal for applications like low-power devices and high-speed processors.
Silicon Wafer in Renewable Energy
The silicon wafer has also become a cornerstone of the renewable energy sector, particularly in the production of solar cells. Photovoltaic (PV) cells, which convert sunlight into electricity, are typically built on silicon wafers.
The Rise of Solar Power
In the 1970s, researchers began exploring silicon wafers for solar energy applications. By the 2000s, advancements in wafer manufacturing reduced the cost of solar panels, making renewable energy more accessible to businesses and consumers.
Efficiency Improvements
Modern solar cells achieve efficiency rates of over 20%, thanks to innovations in silicon wafer design. Techniques like surface texturing and passivation have optimized the ability of silicon wafers to capture and convert sunlight.
The Future of Silicon Wafer Technology
As the demand for advanced electronics and renewable energy solutions grows, the silicon wafer will continue to evolve. Here are some key trends shaping the future of silicon wafer technology:
Larger and Thinner Wafers
Manufacturers are exploring the possibility of producing 18-inch (450 mm) wafers to further reduce costs and increase chip yields. At the same time, thinner wafers are being developed to minimize material waste and improve sustainability.
Advanced Materials
While silicon remains the dominant material for wafers, alternative materials like silicon carbide (SiC) and gallium nitride (GaN) are gaining attention for specific applications, such as high-power electronics and radio-frequency devices
Quantum Computing
The development of quantum computers relies on highly specialized silicon wafers to support qubits. These wafers must meet extremely stringent requirements for purity and structural integrity.
The Comprehensive Guide to Silicon Wafers: Everything You Need to Know
Silicon wafers are a foundational element of modern technology, playing a pivotal role in a wide range of industries, from electronics to renewable energy. These thin slices of silicon are the building blocks of semiconductors and integrated circuits, making them essential for devices like computers, smartphones, and solar panels.
This comprehensive guide explores what silicon wafers are, how they’re made, their applications, and their significance in various industries. By the end, you’ll have a complete understanding of silicon wafers and why they are so critical to modern life.
What Are Silicon Wafers?
Silicon wafers are ultra-thin, flat discs made from crystalline silicon. They serve as the substrate upon which microelectronic circuits and other devices are built. Silicon, a semiconducting material, is chosen for its ability to control electrical conductivity, a property that makes it ideal for manufacturing electronic components.
Silicon wafers are meticulously crafted to meet the exacting standards required in modern electronics. Each wafer must be free from imperfections to ensure the reliability and performance of the devices built upon it. From the smallest transistors in microchips to photovoltaic cells in solar panels, silicon wafers are a key component.
The Importance of Silicon Wafers in Technology
Modern technology would not exist without silicon wafers. They are integral to the development of semiconductors, the “brains” of electronic devices. Without semiconductors, the devices we rely on daily—such as smartphones, laptops, and medical equipment—would not function.
In addition to electronics, silicon wafers play a crucial role in renewable energy technologies. Solar panels, for instance, rely on silicon wafers to capture sunlight and convert it into electricity. The demand for efficient and cost-effective energy solutions has further increased the importance of silicon wafers in recent years.
The versatility and efficiency of silicon wafers make them indispensable across industries, solidifying their role as a cornerstone of technological advancement.
How Are Silicon Wafers Made?
The production of silicon wafers is a highly specialized process that combines advanced technology with meticulous precision. Below is an in-depth look at each stage of the manufacturing process:
Silicon Refinement
The journey begins with silicon, the second most abundant element on Earth. Raw silicon is extracted from quartz and purified to remove impurities. This creates metallurgical-grade silicon, which is then further refined to produce electronic-grade silicon with a purity level of 99.9999%.
Crystal Growth
The purified silicon is melted, and a small seed crystal is dipped into the molten silicon. Using the Czochralski (CZ) process, the seed crystal is slowly pulled out while rotating, forming a large cylindrical silicon ingot. This ingot consists of a single crystal structure, essential for the electrical properties of silicon wafers.
Slicing the Ingot
The silicon ingot is sliced into thin wafers using precision diamond wire saws. Each wafer is cut to a specific thickness, typically between 200 and 300 microns. The slicing process must ensure uniformity to maintain consistency in the wafers’ performance.
Polishing and Cleaning
After slicing, the wafers undergo a polishing process to create a smooth, defect-free surface. This step is critical, as imperfections can interfere with the functionality of electronic components. The wafers are then cleaned to remove any residual particles.
Doping
Doping involves introducing impurities, such as boron or phosphorus, into the silicon wafer. This process alters the wafer’s electrical properties, making it either n-type (negative) or p-type (positive). The doping process enables the wafers to conduct electricity under specific conditions.
Testing and Quality Control
Each silicon wafer is rigorously tested to ensure it meets strict quality standards. Advanced inspection techniques detect even microscopic defects, ensuring that only high-quality wafers proceed to the next stages of production.
Applications of Silicon Wafers
Silicon wafers are used in a variety of applications, each requiring specific properties and performance characteristics. Let’s explore the most common uses of silicon wafers:
Microelectronics and Semiconductors
The semiconductor industry is the largest consumer of silicon wafers. Integrated circuits (ICs), which power computers, smartphones, and other devices, are built on silicon wafers. These wafers serve as the platform for creating transistors, diodes, and other electronic components.
Solar Energy
Silicon wafers are critical in the production of photovoltaic (PV) cells, which are the building blocks of solar panels. These cells capture sunlight and convert it into electricity, providing a renewable energy source for homes and businesses.
MEMS Devices
Microelectromechanical systems (MEMS) devices, such as accelerometers, gyroscopes, and pressure sensors, rely on silicon wafers for their construction. MEMS technology is used in automotive systems, medical devices, and consumer electronics.
Optoelectronics
Silicon wafers are also used in optoelectronic devices, including light-emitting diodes (LEDs), photodetectors, and image sensors. These applications demonstrate the versatility of silicon wafers in both consumer and industrial technologies.
Advanced Computing
In high-performance computing applications, silicon wafers are used to fabricate processors and memory chips that drive cutting-edge technologies like artificial intelligence (AI), machine learning, and data centers.
Types of Silicon Wafers
Silicon wafers come in various types, tailored to specific applications. The most common types include:
- Monocrystalline Silicon Wafers
Made from a single crystal structure, these wafers offer superior electrical properties and are widely used in high-performance electronics and solar cells. - Polycrystalline Silicon Wafers
Composed of multiple silicon crystals, these wafers are less expensive and are commonly used in cost-sensitive applications like solar panels. - SOI (Silicon-On-Insulator) Wafers
These wafers have an insulating layer between the silicon substrate and the device layer, enabling improved performance and reduced power consumption in microelectronic devices. - Doped Wafers
These wafers are specially treated to modify their electrical properties, making them suitable for specific semiconductor applications.
Challenges in Silicon Wafer Production
The production of silicon wafers is not without challenges. Here are some of the primary obstacles manufacturers face:
- Cost and Complexity
The high cost of equipment and the complexity of the manufacturing process make silicon wafer production a significant investment. - Defect Management
Even the smallest defect in a silicon wafer can affect the performance of the final product. Maintaining a defect-free manufacturing environment is critical. - Environmental Impact
The production of silicon wafers consumes significant energy and water, raising concerns about sustainability. Efforts are underway to minimize the environmental footprint of the manufacturing process.
Future Trends in Silicon Wafer Technology
The evolution of silicon wafer technology continues to shape the future of electronics and energy. Here are some emerging trends:
Smaller Node Sizes
As semiconductor technology advances, silicon wafers must accommodate smaller and more complex transistors. This trend drives innovation in wafer fabrication techniques.
Recycling and Sustainability
With a growing focus on sustainability, manufacturers are exploring ways to recycle silicon wafers and reduce waste. These efforts are critical for minimizing the environmental impact of the industry.
Hybrid Materials
Research into hybrid materials, such as silicon carbide (SiC) and gallium nitride (GaN), aims to complement silicon wafers in high-performance applications.
Quantum Computing
The development of quantum computers relies on silicon wafers with unique properties to support quantum bits (qubits). This represents a new frontier for wafer technology.
50mm-300mm Silicon Wafers
Silicon Valley Microelectronics provides different diameter silicon wafers (300mm, 200mm, 150mm, 125mm, 100mm, 76mm, and 50mm) in a variety of specifications, suitable for a wide range of applications.
You can find our inventory of the different diameters we offer through the links here: 300mm, 200mm, 150mm, 125mm, 100mm, 76mm, 50mm
Double Side Polished Wafers (DSP)
Silicon Valley Microelectronics uses simultaneous double-side polishing technology, and therefore can supply a wide variety of high-quality ultra-flat wafers to meet the exact controlled flatness requirements of each customer.
Ultra Flat Wafers
Silicon Valley Microelectronics can supply a wide variety of high-quality ultra-flat wafers to meet the exact controlled flatness requirements of each customer.
Float Zone Wafers (FZ)
Silicon Valley Microelectronics offers float zone (FZ) wafers ranging in diameter from 50mm to 200mm. These wafers have a low concentration of impurities and high-temperature capabilities. The properties of FZ wafers give them advantages over CZ wafers in a variety of applications.
Low Resistivity Wafers
Silicon Valley Microelectronics supplies both N-type and P-type low resistivity wafers in all diameters, 50mm to 300mm, with or without backseal. We can achieve resistivity <0.01 ohm-cm.
N-Type Wafers
Silicon Valley Microelectronics supplies a variety of N-type wafers with phosphorus/antimony/arsenic dopant, in diameters ranging from 50mm to 300mm.
Coinroll Wafers
Silicon Valley Microelectronics offers a variety of 200mm and 300mm coinroll wafers.
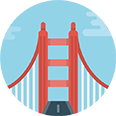
Anywhere in the Bay Area within 4 hours.
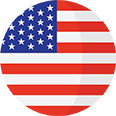
In the United States within 1 day.
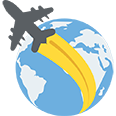
Internationally within 3 days.